Anodic alumina plate process: on the shelf a degreasing ~water washing ~alkali corrosion ~water washing ~neutralization and water washing anodic oxidation water washing hole water washing shelf detection packaging.
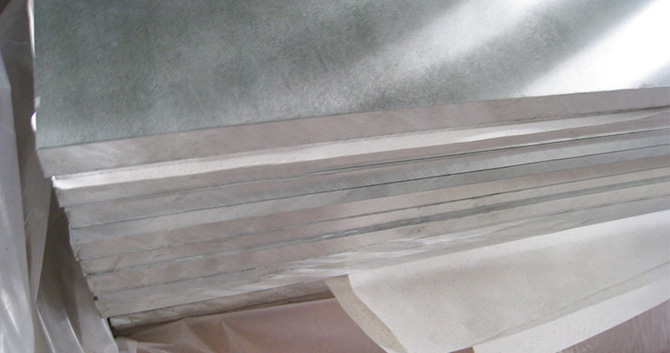
Degreasing, alkali corrosion, neutralization, anodic oxidation, sealing and other processes are the key to ensure the quality of oxidation treatment.
Many customers will require the aluminum plate to be oxidized. Why do most customers have to do this processing step? What are the benefits?
(1) Good processability: the positive anodized aluminum plate has strong decorative, moderate hardness, easy bending and forming, continuous high-speed stamping, convenient for direct processing into products, no need for complex surface treatment, greatly shorten the production cycle of products and reduce production costs.
(2) Weather resistance is good: standard thickness of oxide film (3 micron) of anodized aluminum plate indoor use for a long time does not change color, corrosion, oxidation, rust. Anodic alumina sheets with a thicker oxide film (10 micron) can be used outdoors and remain colourless under long-term exposure to sunlight.
(3) Metal sensitivity: Anodized aluminium sheet plate has high surface hardness, gem grade, good scratch resistance, no paint covering, retaining the metal color of aluminium sheet, highlighting modern metal sensitivity, improving product grade and added value.
(4) High fire resistance: pure metal products, no paint and any chemical substances on the surface, 600 degrees high temperature, no combustion, no toxic gases, in line with the requirements of fire protection and environmental protection.
(5) Strong anti-fouling: no fingerprints, no stains, easy to clean, no corrosion spots.
(6) Strong applicability: wide application, suitable for sheet metal aluminum ceiling,aluminium curtain wall panel, aluminum-plastic panel, fire-proof panel, honeycomb aluminum panel, aluminum veneer, electrical panel, cabinet panel, furniture panel, etc.